O French Solar Energy Institute Inés desenvolveu novos módulos fotovoltaicos con termoplásticos e fibras naturais procedentes en Europa, como o liño e o basalto. Os científicos teñen como obxectivo reducir a pegada ambiental e o peso dos paneis solares, ao tempo que melloran o reciclaxe.
Un panel de vidro reciclado na parte dianteira e un composto de liño na parte traseira
Imaxe: GD
Da revista PV Francia
Os investigadores do Instituto Nacional de Enerxía Solar de Francia (INES)-unha división da Comisión de Enerxías Alternativas e Enerxía Atómica (CEA) francesa-están a desenvolver módulos solares con novos materiais baseados en bio nos lados dianteiros e traseiros.
"Como a pegada de carbono e a análise do ciclo de vida convertéronse agora en criterios esenciais na elección dos paneis fotovoltaicos, o abastecemento de materiais converterase nun elemento crucial en Europa nos próximos anos", dixo Anis Fouini, o director de CEA-ILES , nunha entrevista coa revista PV Francia.
Aude Derrier, a coordinadora do proxecto de investigación, dixo que os seus compañeiros miraron os diversos materiais que xa existen, para atopar un que poida permitir aos fabricantes de módulos producir paneis que melloren o rendemento, a durabilidade e o custo, ao tempo que reduce o impacto ambiental. O primeiro demostrador consiste en células solares de heterojunción (HTJ) integradas nun material composto.
"O lado dianteiro está feito dun polímero cheo de fibra de vidro, que proporciona transparencia", dixo Derrier. "A parte traseira está feita de composto baseado en termoplásticos nos que se integrou un tecido de dúas fibras, liño e basalto, que proporcionará forza mecánica, pero tamén unha mellor resistencia á humidade."
O liño provén do norte de Francia, onde xa está presente todo o ecosistema industrial. O basalto provén noutros lugares de Europa e é tecido por un socio industrial de Inés. Isto reduciu a pegada de carbono en 75 gramos de CO2 por vatio, en comparación cun módulo de referencia da mesma potencia. O peso tamén foi optimizado e é inferior a 5 quilogramos por metro cadrado.
"Este módulo está dirixido ao PV do tellado e á integración de edificios", dixo Derrier. "A vantaxe é que ten unha cor naturalmente negra, sen necesidade dunha folla traseira. En termos de reciclaxe, grazas aos termoplásticos, que se poden remitir, a separación das capas tamén é máis sinxela. "
O módulo pódese facer sen adaptar os procesos actuais. Derrier dixo que a idea é transferir a tecnoloxía aos fabricantes, sen investimento adicional.
"O único imperativo é ter conxeladores para almacenar o material e non comezar o proceso de reticulación de resinas, pero a maioría dos fabricantes hoxe usan pre-pre-pre-pre-pre-están equipados para iso", dixo.
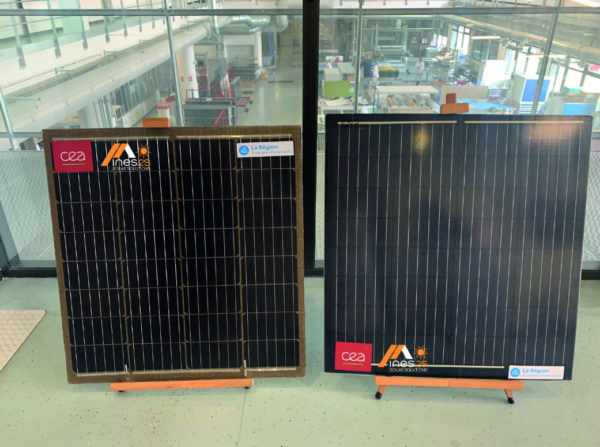
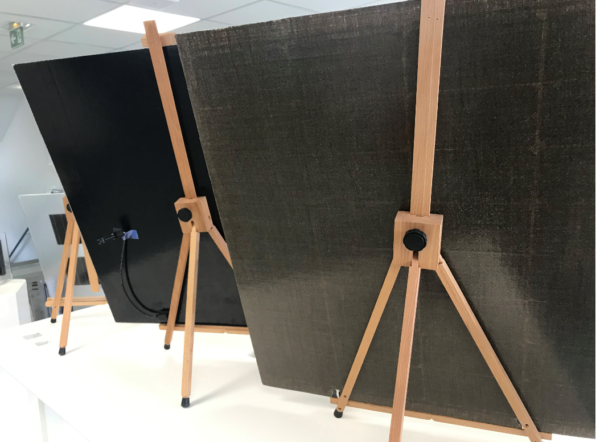
"Traballamos na segunda vida de vidro e desenvolvemos un módulo composto por vidro reutilizado de 2,8 mm que provén dun vello módulo", dixo Derrier. "Tamén empregamos un encapsulante termoplástico que non require reticulación, que polo tanto será fácil de reciclar e un composto termoplástico con fibra de liño para resistencia."
A cara traseira libre de basalto do módulo ten unha cor natural de liño, que podería ser esteticamente interesante para os arquitectos en termos de integración de fachadas, por exemplo. Ademais, a ferramenta de cálculo de INES mostrou unha redución do 10% na pegada de carbono.
"Agora é imprescindible cuestionar as cadeas de subministración fotovoltaicas", dixo Jouini. "Coa axuda da rexión de Ródano-Alpes no marco do Plan Internacional de Desenvolvemento, polo tanto fomos buscar xogadores fóra do sector solar para atopar novos termoplásticos e novas fibras. Tamén pensamos no proceso de laminación actual, moi intensivo en enerxía. "
Entre a presurización, a prensado e a fase de refrixeración, a laminación adoita ter unha duración entre 30 e 35 minutos, cunha temperatura de funcionamento de aproximadamente 150 C a 160 C.
"Pero para os módulos que incorporan cada vez máis materiais deseñados eco, é necesario transformar os termoplásticos en torno a 200 C a 250 C, sabendo que a tecnoloxía HTJ é sensible á calor e non debe exceder os 200 C", dixo Derrier.
O Instituto de Investigación está a unir a Roctool especialista en termocompresión de indución baseado en Francia para reducir os tempos de ciclo e facer formas segundo as necesidades dos clientes. Xuntos, desenvolveron un módulo cunha cara traseira feita de composto termoplástico de tipo polipropileno, ao que se integraron fibras de carbono recicladas. O lado dianteiro está feito de termoplásticos e fibra de vidro.
"O proceso de termocompresión de indución de Roctool fai posible quentar as dúas placas dianteiras e traseiras rapidamente, sen ter que chegar a 200 C no núcleo das células HTJ", dixo Derrier.
A compañía afirma que o investimento é menor e que o proceso podería conseguir un tempo de ciclo de só uns minutos, mentres usa menos enerxía. A tecnoloxía está dirixida a fabricantes compostos, para darlles a posibilidade de producir partes de diferentes formas e tamaños, á vez que integran materiais máis lixeiros e máis duradeiros.
Tempo de publicación: xuño 24-2022